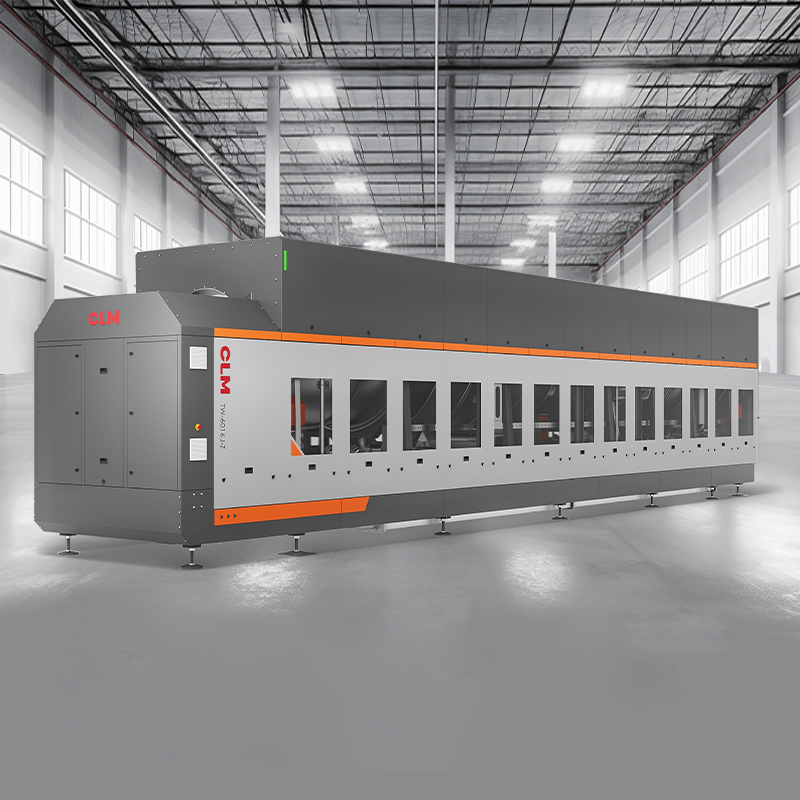
Tuunl Washer Body
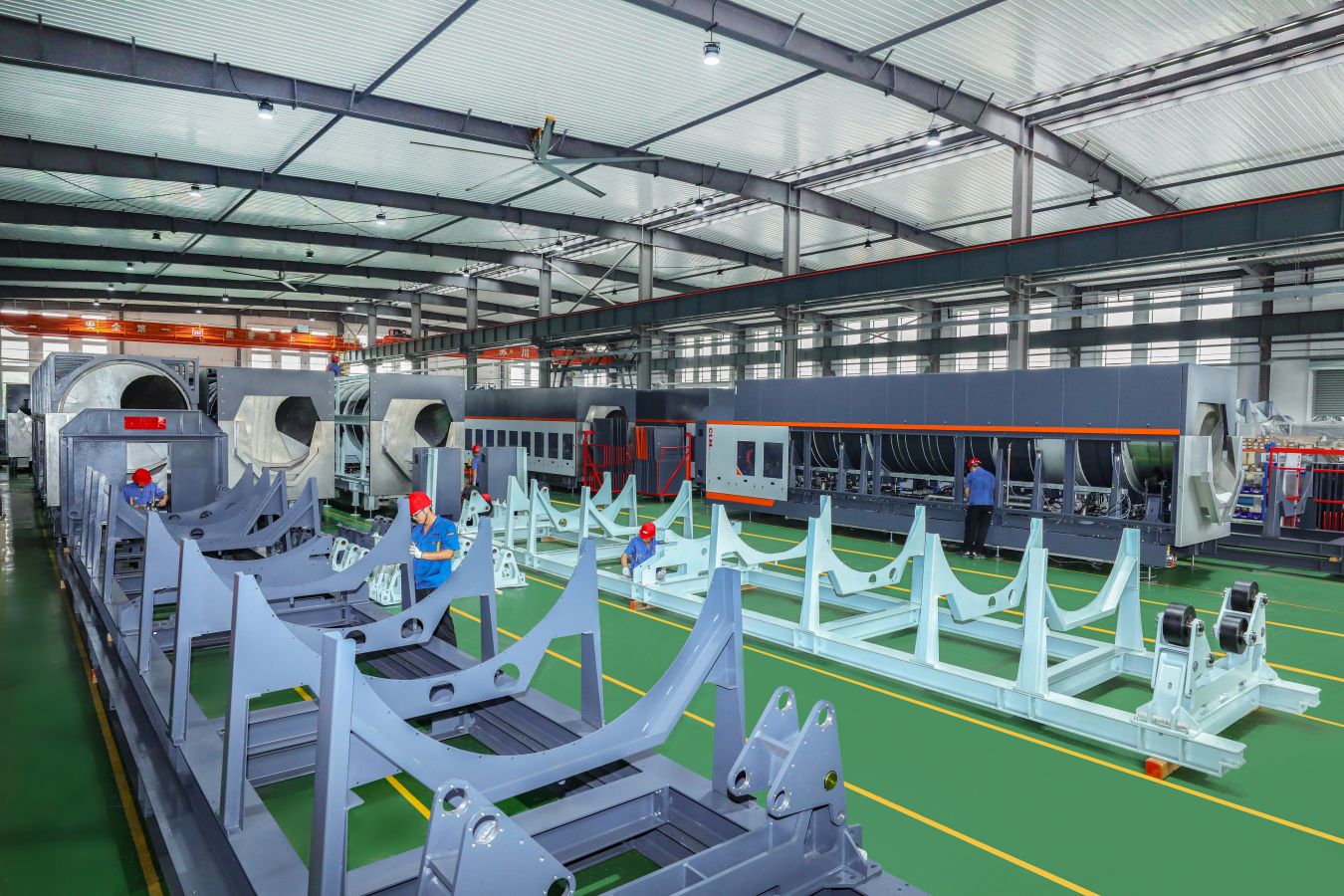
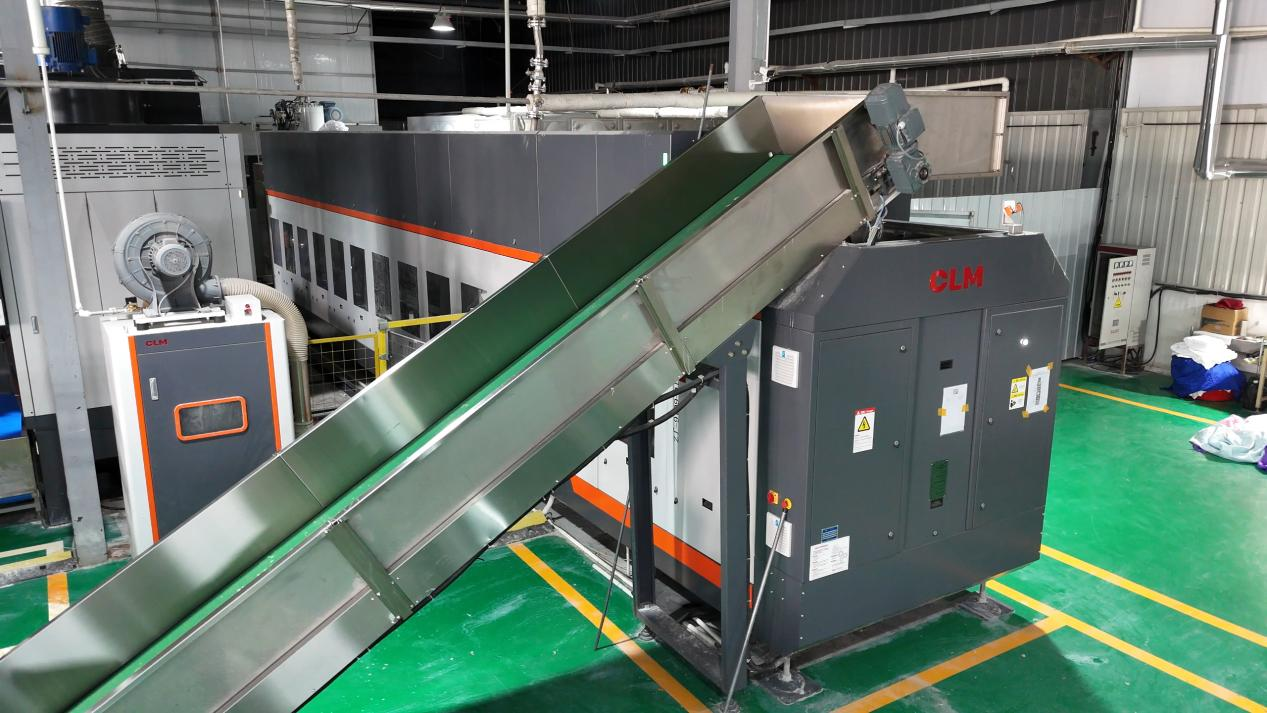
Technical Parameter
Configurations and models
Technical parameters
Configurations and models
Wash Configuration | Standards | Professional | Intellectual Cloud | |||
60 kg | 80 kg | 60 kg | 80 kg | 60 kg | 80 kg | |
Super strong construction, 200 millimeter double beams, hot-dip galvanized. | ▪ | ▪ | ▪ | ▪ | ▪ | ▪ |
Construction of two support frame points | ▪ | ▪ | ▪ | ▪ | ▪ | ▪ |
3-point support, self-balancing support structure construction (16 bunkers and more) | ▪ | ▪ | ▪ | ▪ | ▪ | ▪ |
Mitsubishi PLC control system | ▪ | ▪ | ▪ | ▪ | ▪ | ▪ |
Main drive reducer - German brand SEW. | ▪ | ▪ | ▪ | ▪ | ▪ | ▪ |
Construction of 300x300 stainless steel drainage tank | ▪ | ▪ | ▪ | ▪ | ▪ | ▪ |
Single cold water inlet pipe | ▪ | ▪ | ▪ | ▪ | ▪ | ▪ |
Stainless Steel Push Button Pipe Construction | ▪ | ▪ | ▪ | ▪ | ▪ | ▪ |
Simple hair filtration device | ▪ | ▪ | ▪ | ▪ | ▪ | ▪ |
Fully automatic hair filtration system | ▪ | ▪ | ▪ | ▪ | ▪ | ▪ |
An inlet hole and a single-row washing structure | ▪ | ▪ | ▪ | ▪ | ▪ | ▪ |
The washing bunker is a single bunker, a perforated partition of the anti-regular washing structure | ▪ | ▪ | ▪ | ▪ | ▪ | ▪ |
The 4-section washing division - all double sections with a counter-mounted washing structure. | ▪ | ▪ | ▪ | ▪ | ▪ | ▪ |
All section joints are manufactured in China. | ▪ | ▪ | ▪ | ▪ | ▪ | ▪ |
All section joints are imported from Germany. | ▪ | ▪ | ▪ | ▪ | ▪ | ▪ |
All electrical components are well-known national brands | ▪ | ▪ | ▪ | ▪ | ▪ | ▪ |
Technical parameters
Name | TW-6016J-B | TW-6016J-Z | TW-8014J-Z | TW-6013J-Z | TW-6012J-Z | TW-6010J-Z | TW-6008J-Z |
Number of bunkers | 16 | 16 | 14 | 13 | 12 | 10 | 8 |
Nominal washing productivity in bunker (kg) | 60 | 60 | 80 | 60 | 60 | 60 | 60 |
Inlet pipe diameter | DN65 | DN65 | DN65 | DN65 | DN65 | DN65 | DN65 |
Inlet pressure (bar) | 2.5~4 | 2.5~4 | 2.5~4 | 2.5~4 | 2.5~4 | 2.5~4 | 2.5~4 |
Inlet pipe diameter for torque | DN50 | DN50 & DN25 | DN50 & DN25 | DN50 & DN25 | DN50 & DN25 | DN50 | DN50 & DN25 |
Steam pressure at inlet (bar) | 4~6 | 4~6 | 4~6 | 4~6 | 4~6 | 4~6 | 4~6 |
Compressed air pressure at the inlet (bar) | 5~8 | 5~8 | 5~8 | 5~8 | 5~8 | 5~8 | 5~8 |
Connected power (kW) | 36.5 | 36.5 | 43.35 | 28.35 | 28.35 | 28.35 | 28.35 |
Voltage (V) | 380 | 380 | 380 | 380 | 380 | 380 | 380 |
Water consumption (kg/kg) | 4.7~5.5 | 4.7~5.5 | 4.7~5.5 | 4.7~5.5 | 4.7~5.5 | 4.7~5.5 | 4.7~5.5 |
Electricity consumption (kWh/h) | 15 | 15 | 16 | 12 | 11 | 10 | 9 |
Steam flow rate (kg/kg) | 0.3~0.4 | 0.3~0.4 | 0.3~0.4 | 0.3~0.4 | 0.3~0.4 | 0.3~0.4 | 0.3~0.4 |
Weight (kg) | 16930 | 17120 | 17800 | 14890 | 14390 | 13400 | 12310 |
Machine dimensions (W×H×D) mm | 3278x2224x14000 | 3278x2224x14000 | 3426x2360x 14650 | 3304x2224x 11820 | 3304x2224x11183 | 3200x2224x9871 | 3200x2245x8500 |
Cold water | DN65 | DN65 | DN65 | DN65 | DN65 | DN65 | DN65 |
Hot water | DN40 | DN40 | DN40 | DN40 | DN40 | DN40 | DN40 |
Drainage | DN125 | DN125 | DN125 | DN125 | DN125 | DN125 | DN125 |
YT-H Heavy 60KG/80KG Press Of Tunnel Washer
1.jpg)
Extraction Press of Clothes Medium 60kg
Tumble Dryer
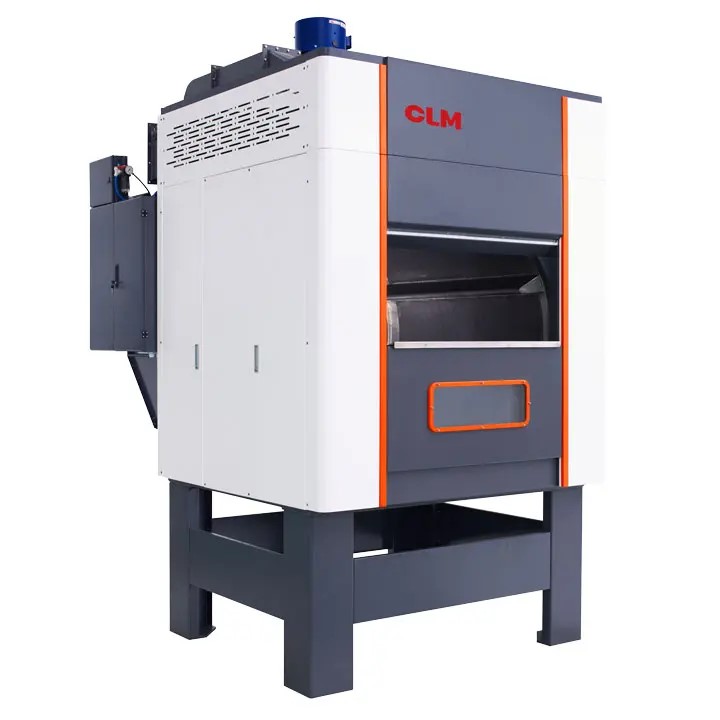
GHG-120Z Series Tumble Dryer

GHG-R Series Tumble Dryer-60R/120R
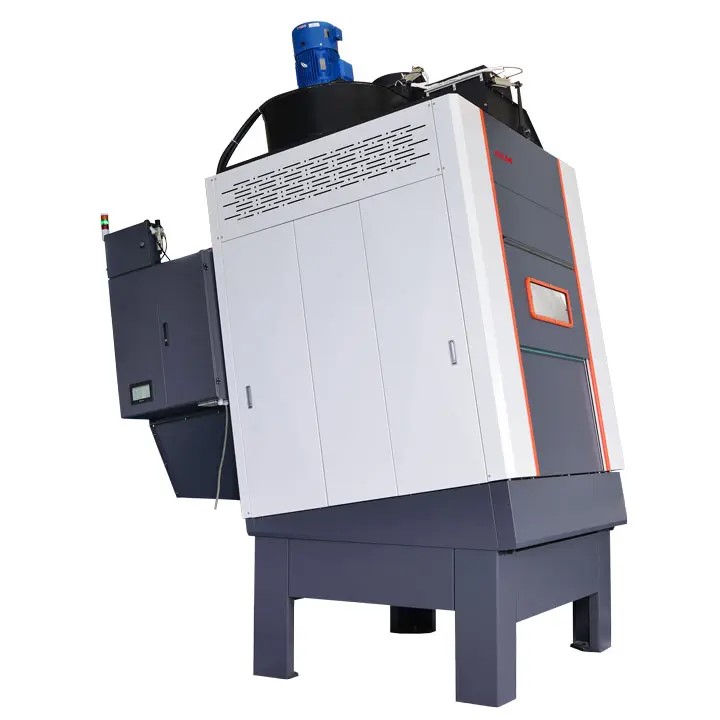
GHG-R Series Tumble Dryer-60R/120R
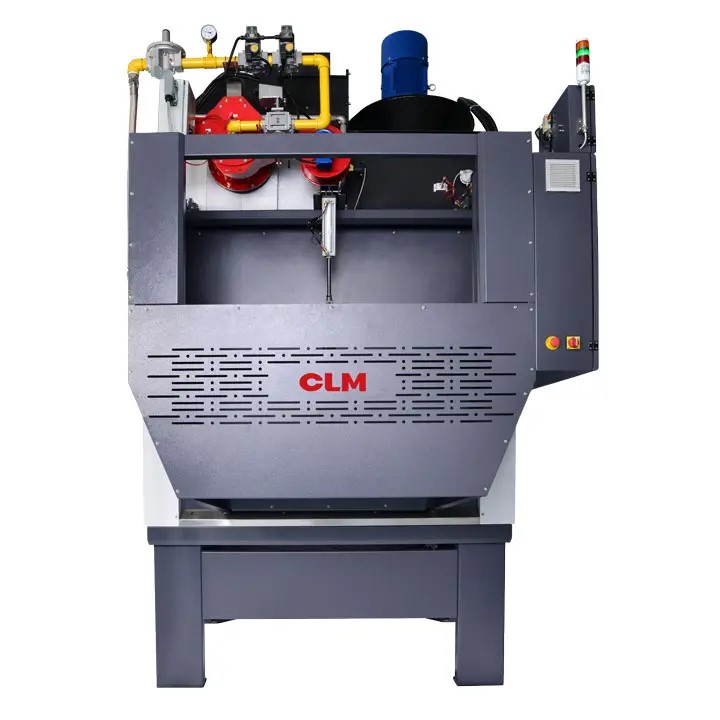
GHG-R Series Tumble Dryer-60R/120R
Other Equipment
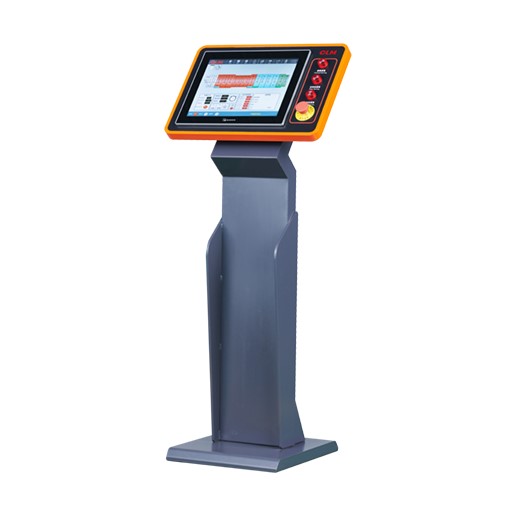
Control System
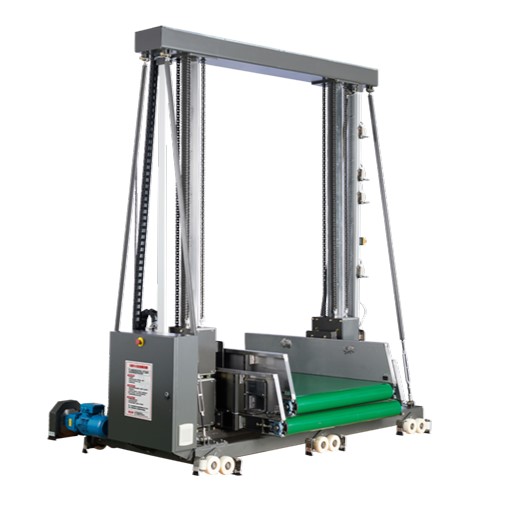
Shuttle Machine
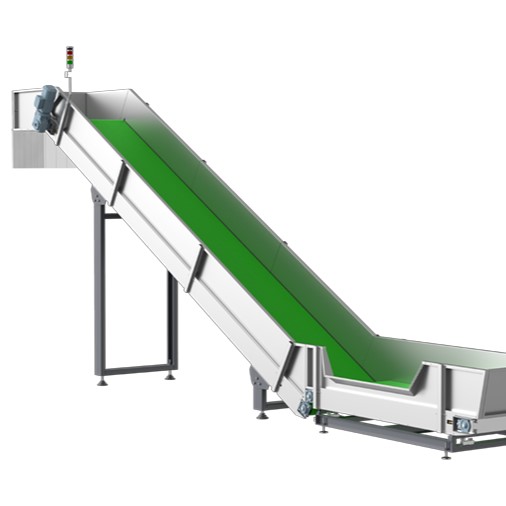
Wheel Loaders
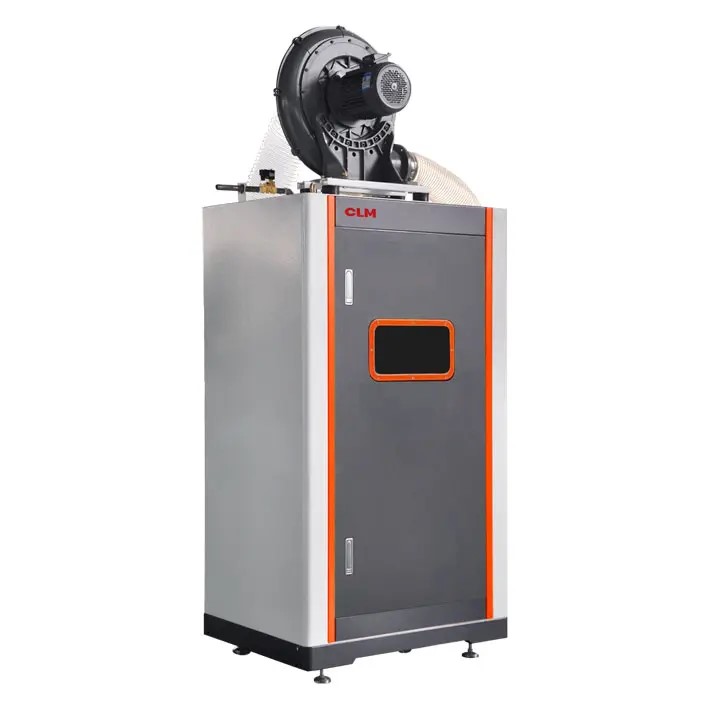
Lint Collector
About Us
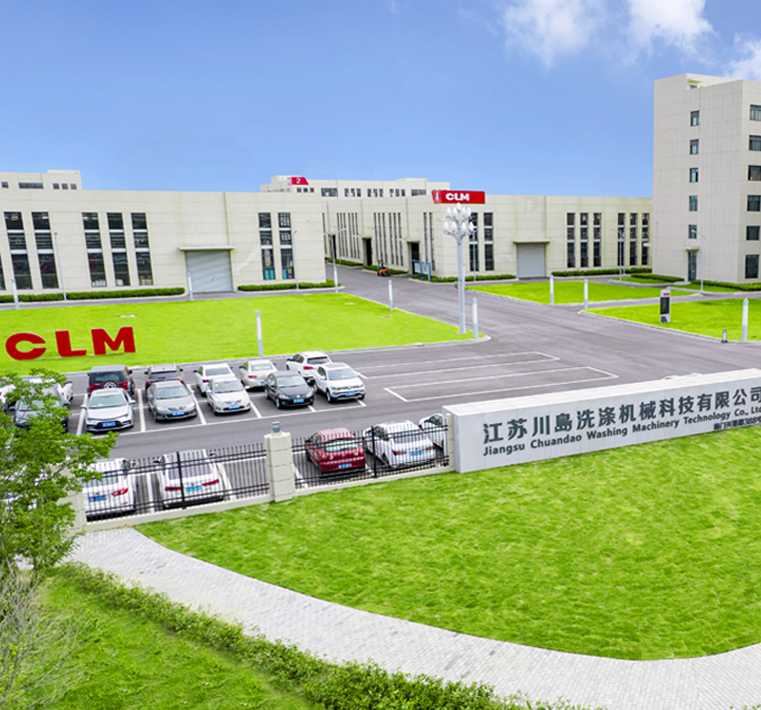