Behind the hotel operation, the cleanliness and hygiene of the linen are directly related to the experience of the hotel guests. It is the key to measuring the quality of the hotel service. The laundry plant, as the professional backing of the hotel linen washing, forms a close ecological chain with the hotel. However, in daily cooperation, many hotel customers have some misunderstandings which have a negative impact on the washing quality of the linen and mutual trust. Today, let’s uncover the secrets of hotel linen washing.
Common Misunderstanding of Hotel Customers
❒ Misunderstanding 1: Linen laundry should be 100% qualified
Hotel linen washing is not just a simple mechanical operation. It is subject to a variety of factors. The linen laundry industry is similar to “special processing of supplied materials”. The degree of pollution of linen is closely related to the type of linen, material, washing mechanical force, detergents, logistics and transportation, seasonal changes, consumption habits of residents, and so on. The final laundry effect always fluctuates in a certain range.
● If people blindly pursue a 100% pass rate, it means that most (97%) of the linen will be “over-washed”, which not only shortens the service life of the linen but also makes the washing cost soar. It is obviously not the most sensible economic choice. In fact, in the laundry industry, less than 3% of the rewashing rate is allowed. (according to the total number of samples). It is a reasonable range after careful consideration.
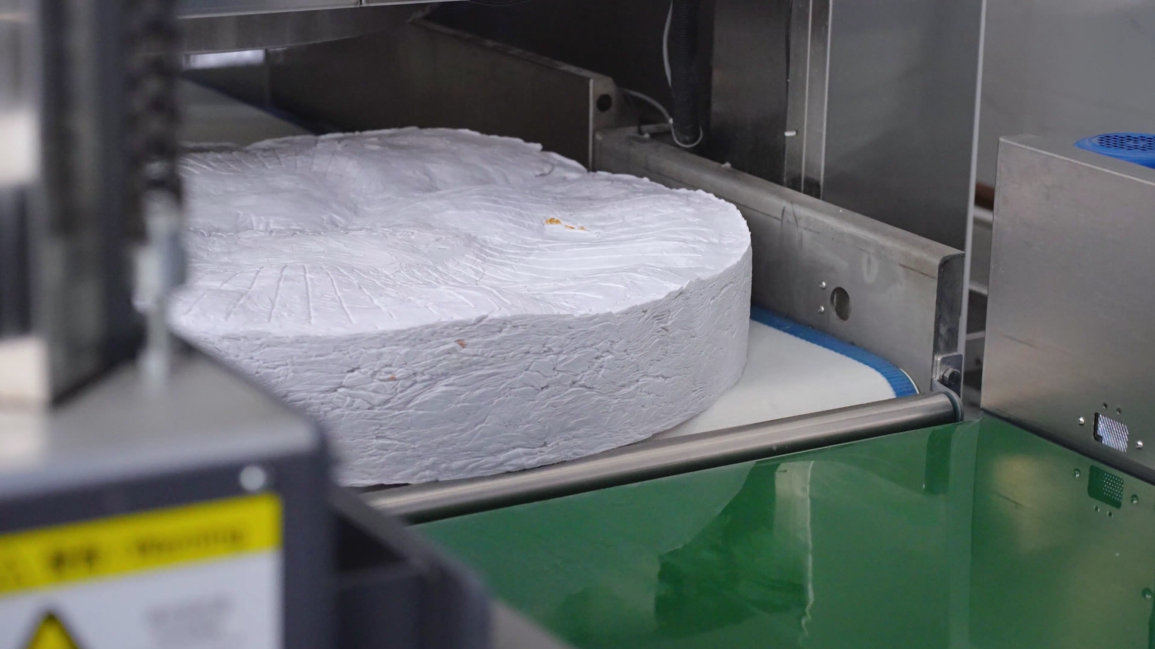
❒ Misunderstanding 2: The breakage rate of linen should be reduced to a minimum after washing
It is generally recommended that the hotel control the damage rate at no more than 3‰ (according to the total number of samples), or reserve 3‰ of the room income as the budget for updating the linen. In recent years, some new linen of the same brand has been much easier to be damaged than old linen, the root cause is the difference in fiber strength.
Although the laundry plant can properly reduce the mechanical pressure of dehydration to reduce damage, the effect is limited ( reducing mechanical force by 20% will extend the average life of less than half a year). As a result, the hotel must pay attention to the key factor of fiber strength when purchasing linen.
❒ Misunderstanding 3: The whiter and softener linen is better.
As cationic surfactants, softeners are often used in the final washing process and can remain on towels. Excessive use of softener will damage the water absorption and whiteness of linen and also affect the next washing.
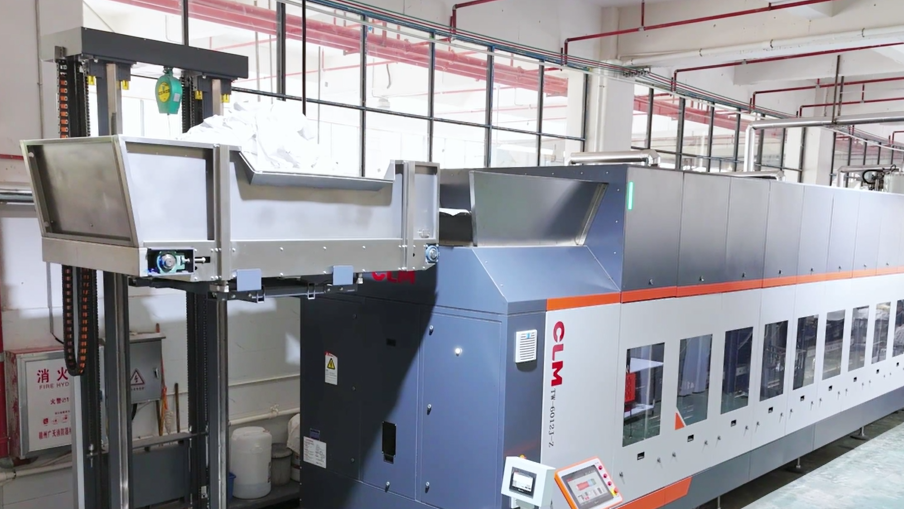
According to incomplete statistics, about 80% of the towels on the market are added to excess softeners, which have negative effects on the towels, the human body, and the environment. Therefore, it is not rational to pursue the extreme softness of towels. The enough softener can be good. More is not always better.
❒Misunderstanding 4: Enough linen ratio will be good.
Insufficient linen ratio has hidden dangers. When the occupancy rate is high, the washing and logistics time is easy to cause a late supply of the linen. High-frequency washing accelerates the aging and damage of linen. Maybe there will be the phenomenon of unqualified linen being temporarily put into use, causing customer complaints. According to relevant statistics, when the linen ratio rises from 3.3par to 4par, the number of linen will increase by 21%, but the overall service life can be extended by 50%, which is the real savings.
Definitely, the ratio adjustment needs to be combined with the occupancy rate of the room type. For example, the outer suburb resort hotel should appropriately increase the linen ratio. It is recommended that the base ratio should be 3 par, the normal ratio should be 3.3 par, and the ideal and economical ratio should be 4 par.
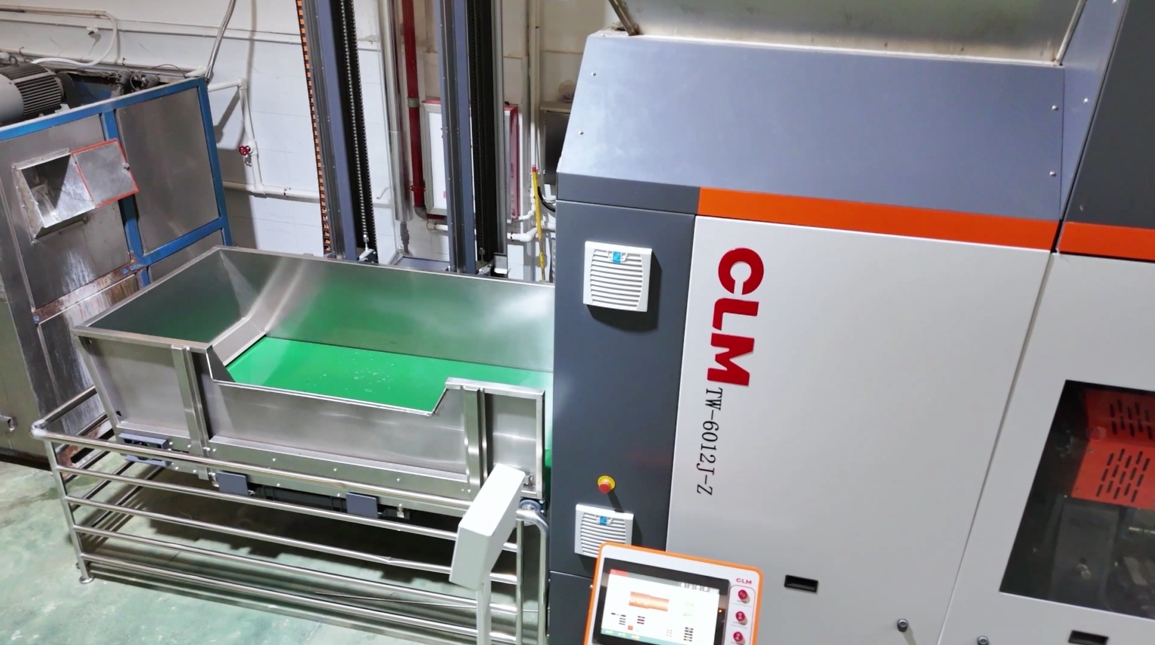
Win-Win Cooperation
In the washing service process, such as turning of quilt covers and pillowcases, linen delivery floor by floor, and other work, the washing plant and the hotel need to consider cost-effectiveness and find the best implementation. They should actively communicate with each other to explore the optimal process. At the same time, simple and efficient working methods should be established, such as marking soiled linen with bags of different colors or labels to ensure that the problem linen is properly handled, avoiding cumbersome processes, and improving overall efficiency.
Conclusion
Service improvement is endless. Cost control can not be ignored as well. Behind many seemingly “free” services, there is a high cost hidden. Only a sustainable cooperation model can last. When the hotel chooses the laundry plant, they focus on the pursuit of quality instead of focusing on the grade. Laundry plants should join hands with the hotels to break misconceptions, improve the quality of hotel linen washing through professional operation and fine management, and bring consistent comfort and peace of mind to guests.
Post time: Jan-06-2025