There are obvious differences in the production efficiency of different laundry factories. These differences are influenced by many factors. These key factors are explored in depth below.
Advanced Equipment: the Cornerstone of Efficiency
The performance, specifications and advancement of the laundry equipment directly affect the production efficiency of a laundry factory. Advanced and adaptive laundry equipment can handle more linen per unit time while maintaining washing quality.
❑ For example, CLM tunnel washer system can wash 1.8 tons of linen per hour with an excellent conservation of energy and water, significantly reducing single wash cycles.
❑ The CLM high-speed ironing line, which is composed of a four-station spreading feeder, super roller ironer, and folder, can reach a maximum operating speed of 60 meters/minute and can handle up to 1200 bed sheets per hour.
These can all help a lot to the efficiency of the laundry factories. According to the industry survey, the overall production efficiency of a laundry factory using high-end laundry equipment is 40%-60% higher than the that of the laundry factory using old equipment, which fully demonstrates the great role of high-quality laundry equipment in promoting efficiency.
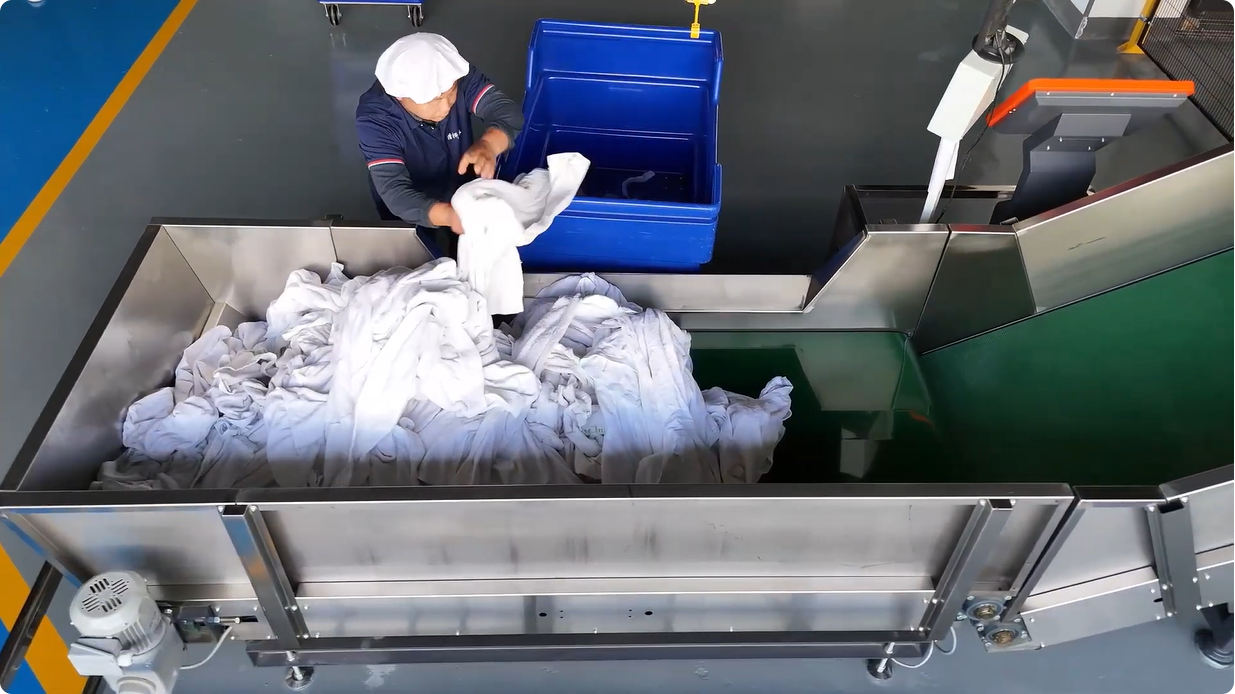
Steam is indispensable in the washing and ironing process of a laundry factory, and steam pressure is a key factor in determining production efficiency. Relevant data show that when the steam pressure is lower than 4.0Barg, most of the chest ironers will not operate normally, resulting in production stagnation. In the range of 4.0-6.0 Barg, though the chest ironer can operate, the efficiency is limited. Only when the steam pressure reaches 6.0-8.0 Barg, the chest ironer can be fully opened and the ironing speed reaches its peak.
❑ For example, after a large laundry plant increased the steam pressure from 5.0Barg to 7.0Barg, its production efficiency of ironing increased by nearly 50%, fully demonstrating the huge influence of steam pressure on the overall efficiency of the laundry plant.
Steam Quality: the Performance Gap between Saturated Steam and Unsaturated Steam
Steam is divided into saturated steam and unsaturated steam. When the steam and water in the pipeline are in a dynamic equilibrium state, it is saturated steam. According to the experimental data, the heat energy transferred by saturated steam is about 30% higher than that of unsaturated steam, which can make the surface temperature of the drying cylinder higher and more stable. In this high temperature environment, the evaporation rate of water inside the linen is significantly accelerated, which greatly improves the ironing efficiency.
❑ Taking the test of a professional washing institution as an example, the use of saturated steam to iron the same batch of linen, the time is about 25% shorter than that of unsaturated steam, which strongly proves the key role of saturated steam in improving efficiency.
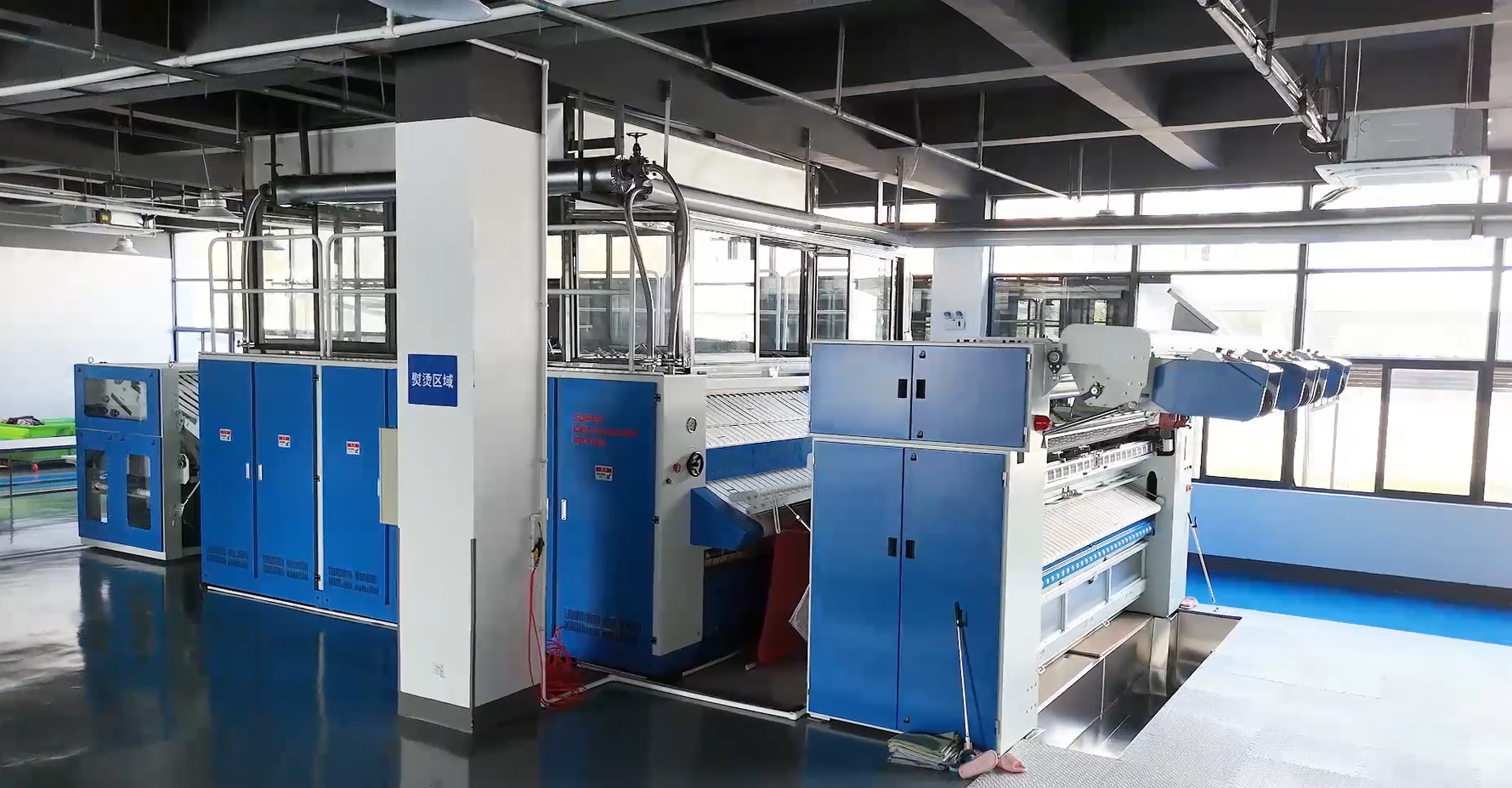
Moisture Control: the Time of Ironing and Drying
The moisture content of the linen is an often overlooked but crucial factor. If the moisture content of the bed sheets and duvet covers is too high, the ironing speed will obviously slow down because the time of evaporating water increases. According to the statistics, every 10% increase in the moisture content of the linen will lead to an increase.
For every 10% increase in the moisture content of the bed sheets and quilt covers, the time of ironing 60kg of bed sheets and quilt covers (the capacity of a tunnel washer chamber is usually 60kg) is extended by an average of 15-20 minutes. As for towels and other highly absorbent linen, when the moisture content is high, their drying time will increase significantly.
❑ CLM heavy-duty water extraction press can control the moisture content of towels under 50%. Using CLM direct-fired tumble dryers to dry 120 kg of towels (equal two pressed linen cakes) only takes 17-22 minutes. If the moisture content of the same towels is 75%, using the same CLM direct-fired tumble dryer to dry them will take an extra 15-20 minutes.
As a result, effectively control the moisture content of the linens has a great significance to improve the production efficiency of laundry plants and save the energy consumption of drying and ironing links.
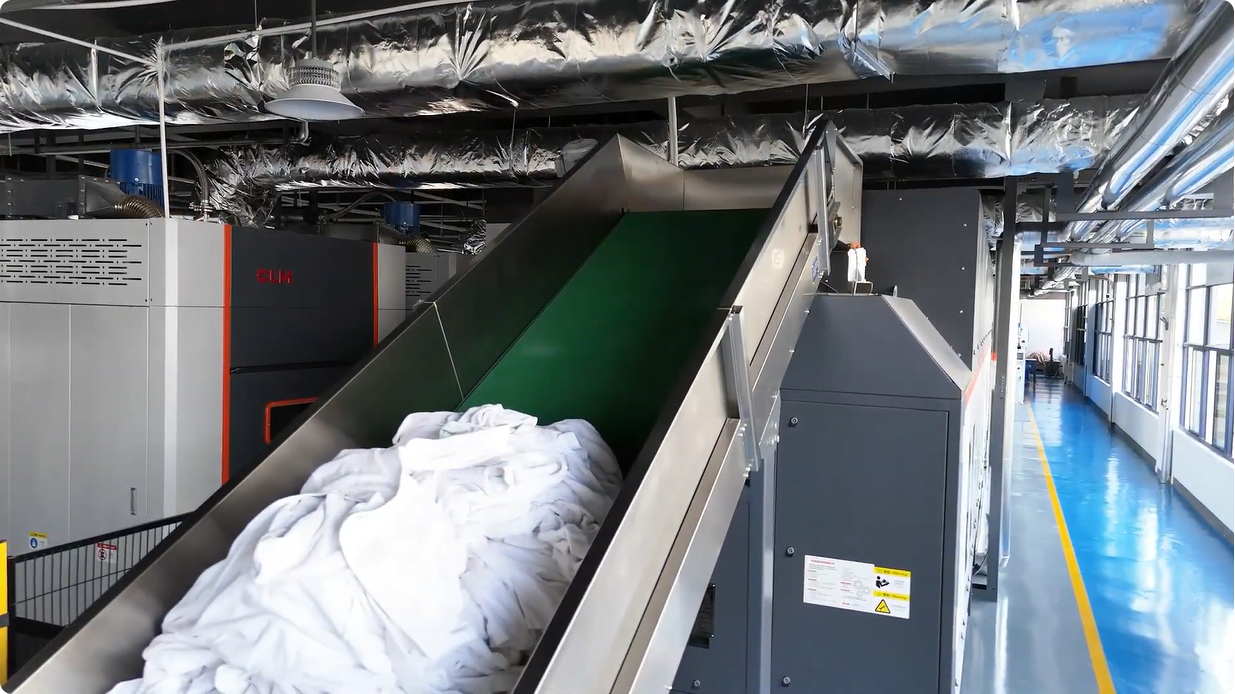
Age of Employees: The Correlation of Human Factors
The high work intensity, long working hours, fewer holidays, and relatively low wages in Chinese laundry factories result in recruitment difficulties. Many factories can only recruit older employees. According to the survey, there is a significant gap between older employees and young employees in terms of operation speed and reaction agility. The average operation speed of old employees is 20-30% slower than that of young employees. This makes it difficult for old employees to keep up with the speed of equipment during the production process, which reduces overall production efficiency.
❑ A laundry plant that introduced a team of young employees reduced the time to complete the same amount of work by about 20%, highlighting the impact of employee age structure on productivity.
Logistics Efficiency: Coordination of Receiving and delivery
The tightness of the time arrangement of the receiving and delivery links directly affects the operation efficiency of the laundry plant. In some laundry plants, there is often a disconnect between washing and ironing because the time of receiving and sending linen is not compact.
❑ For example, when the washing speed doesn’t match the ironing speed, it may lead to the ironing area waiting for the linen in the washing area, resulting in idle equipment and a waste of time.
According to industry data, due to the poor reception and delivery connection, about 15% of the laundry plants have less than 60% of the equipment utilization rate, which seriously restricts the overall production efficiency.
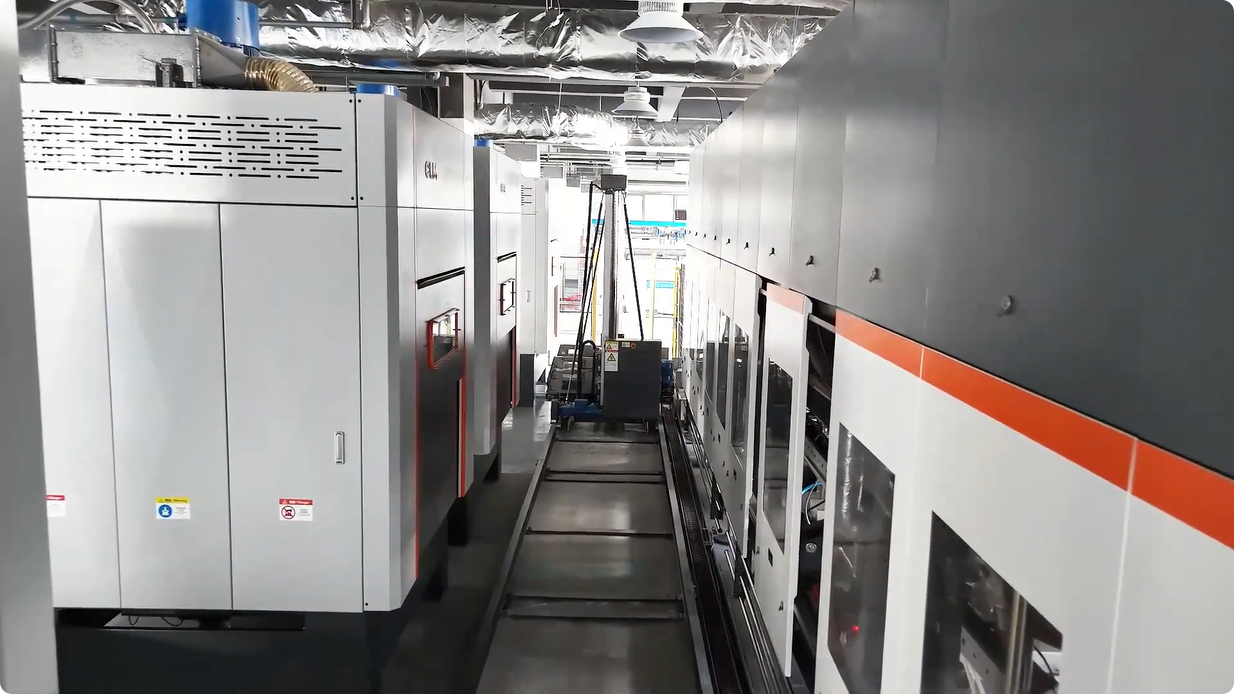
Management Practices: The Role of Incentive and Supervision
The management mode of the laundry plant has a profound influence on production efficiency. The intensity of supervision is directly related to the enthusiasm of employees.
According to the survey, in laundry plants lacking effective supervision and incentive mechanisms, employees’ awareness of active work is weak, and the average work efficiency is only 60-70% of that of factories with good management mechanisms. After some laundry plants adopt the piecework reward mechanism, the enthusiasm of employees is greatly improved. The production efficiency is significantly improved, and the income of employees is correspondingly increased.
❑ For example, after the implementation of the piecework reward system in a laundry plant, the monthly output increased by about 30%, which fully reflects the key value of scientific management in improving the production efficiency of the laundry plant.
Conclusion
All in all, equipment efficiency, steam pressure, steam quality, moisture content, age of employees, logistics and laundry plant management are intertwined, which jointly affect the operating efficiency of the laundry plant.
Laundry plant managers should consider these factors comprehensively and formulate targeted optimization strategies to improve overall production efficiency and market competitiveness.
Post time: Dec-30-2024