The damage caused to the linen by the tunnel washer mainly lies in the welding process of the inner drum. Many manufacturers use gas preservation welding to weld tunnel washers, which is low-cost and highly efficient.
The Drawbacks of Gas Preservation Welding
However, this welding method also has big disadvantages, there will be welding slag splash during the welding process. The inner drum of the tunnel washer is a mesh composed of rows of small holes punched by a stainless steel plate. These splash welding slag particles stick to the edge of the mesh holes above, which has high invisibility, and it isn't easy to clean up thoroughly. Some of them will stick to the inner wall of the mesh, which is also difficult to clean. These splatters of welding slag can easily spoil the linen.
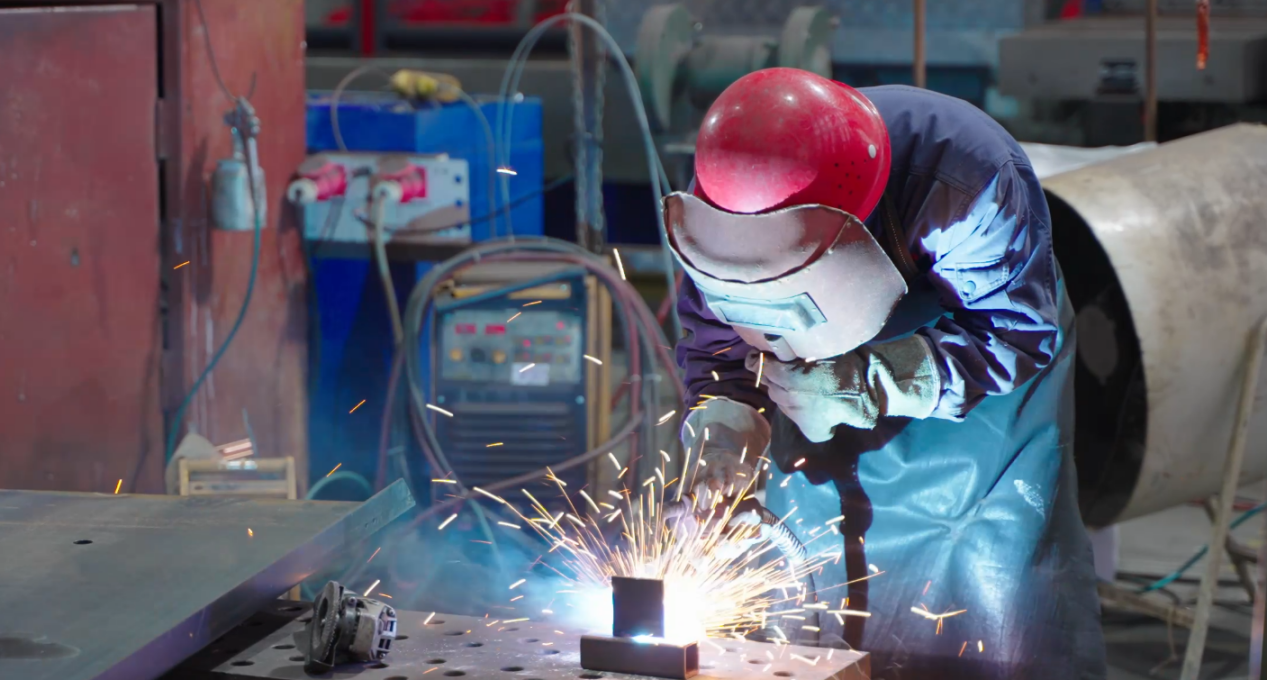
Precision Robotic Welding: The CLM Solution
The inner drum of the CLM tunnel washer, in contact with the linen, is precisely welded by the robot. There are no burrs and spatter in the inner drum. After the welding is completed, people use silk stockings to inspect the drum without dead corners to ensure that the linen will not be damaged.
Insufficient Welding Strength: A Hidden Hazard
Insufficient welding strength can also cause damage to the linen. The inner drum is composed of several stainless steel sheet metal parts by welding. A crack in any one of these parts will cause serious damage to the linen like a sharp knife.
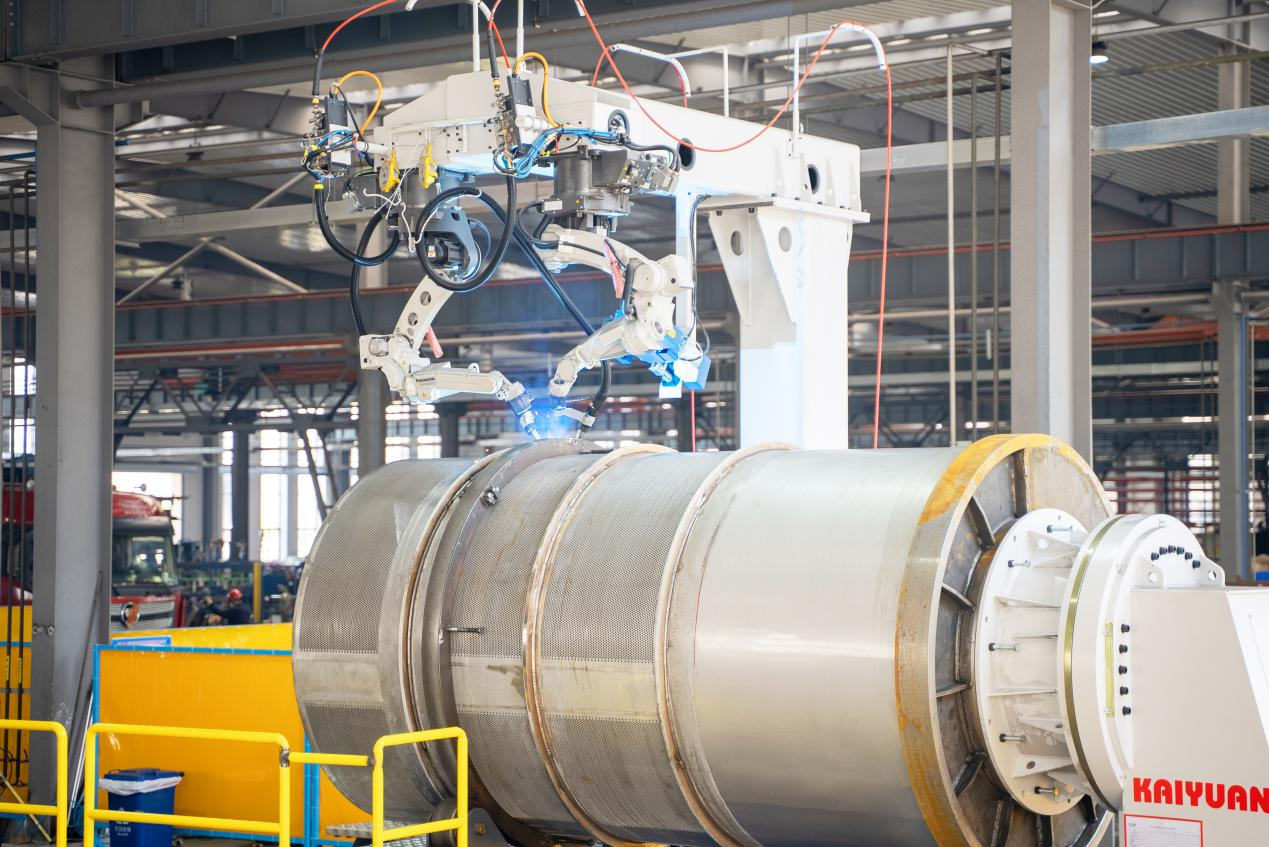
Some tunnel washers’ inner drums are only single-sided welding. The other side is protected with silicone. The docking between the chamber and the chamber is directly welded, and this process makes it difficult to ensure the welding strength. Once a welding site cracks, it will cause serious damage to the linen.
Double-Sided Welding: The CLM Advantage
The CLM inner drum is all welded on both sides. The connection of each chamber is embedded in a 20mm stainless steel flange ring and welded on 3 sides. It ensures the strength and durability of the entire inner cylinder of the laundry dragon.
Post time: Nov-05-2024