Nowadays, environmental protection and sustainable development are the global focus. How to both ensure productivity and reduce the ecological footprint becomes an urgent problem for the laundry industry because laundry plants consume a lot of water, electricity, steam, and other resources.
Haolan, a laundry plant in Hubei Province, China, is the direct-fired laundry factory sample of CLM. It is leading the new trend of green laundry with its innovative technology, highly efficient energy use, and eco-friendly designs.
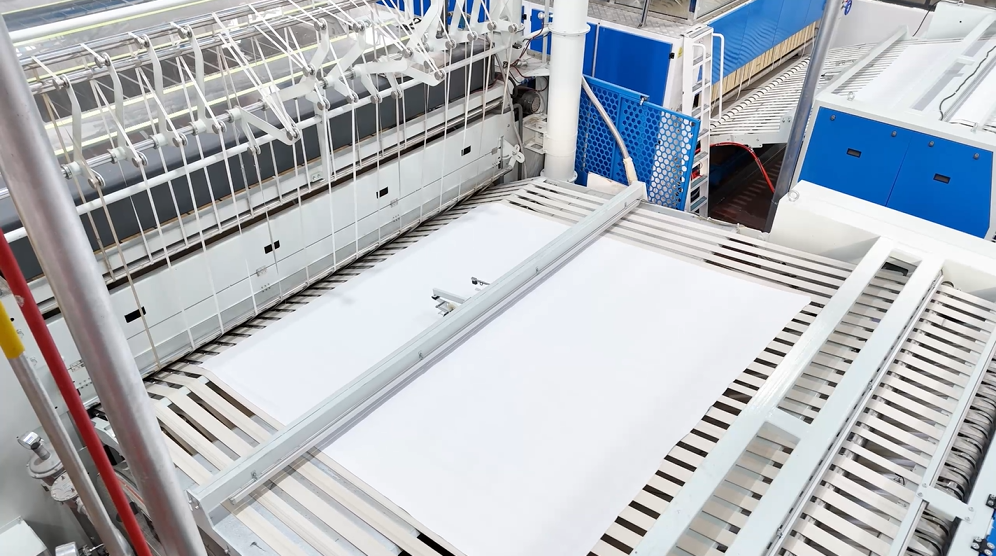
Highly Efficient Direct-fired Drying Technology
CLM’s direct-fired tumble dryer is a star of energy consumption because of its profound and eco-friendly quality. It adapts an Italian Riello high-power eco-friendly burner and can heat the air in the tumble dryer to 220 degrees Celsius in 3 minutes, greatly increasing the heating efficiency. The unique returning air circulation design can effectively recover and recycle the heat from emissions which reduces the energy consumption and increases the drying efficiency. The insulation design reduces the heat loss and further reduces the energy consumption by over 5%.
Green and Eco-friendly Design Concepts
The design concepts of the CLM direct-fired tumble dryers are closely related to environmental protection. The dryer’s inclined discharge design saves more than 30% of discharge time and reduces the risk of mixing up in the laundry plant. In terms of lint collection, the tumble dryer uses two methods to remove the lint thoroughly: the pneumatic method and the vibration method which ensures the circulation of hot air and maintains the drying efficiency. The design of a large air volume and low noise fan realizes low energy consumption and high efficiency.
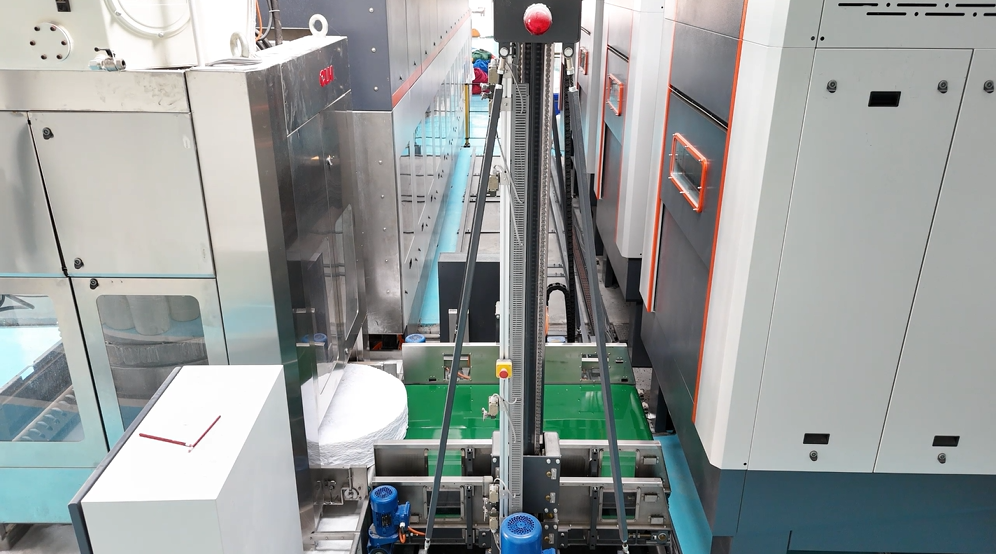
Energy Conservation and Carbon Reduction
The Haolan laundry plant has achieved remarkable results. Compared with traditional steam-heated dryers, direct-fired dryers have improved in terms of energy consumption, efficiency, and environmental protection. Direct-fired dryers don’t require the secondary conversion of heat source, ensuring more energy utilization, lower loss, and higher drying efficiency. According to the statistics of application, under the steam pressure of 6-7 kg, a steam dryer takes 25 minutes and consumes 130 kg of steam to dry100 kg towels with 50% moisture content, while the CLM direct-fired tumble dryer takes only 20 minutes and consumes about 7 cubic meters of natural gas.
Real-time Monitoring and Data Optimization
Haolan Laundry Plant has installed a flow meter to monitor the condition of gas consumption and optimize energy consumption. According to the real-time monitoring, drying 115.6kg of towels consumes 4.6 cubic meters of natural gas, and drying 123kg of towels consumes 6.2 cubic meters of natural gas, showing the high efficiency of the equipment.
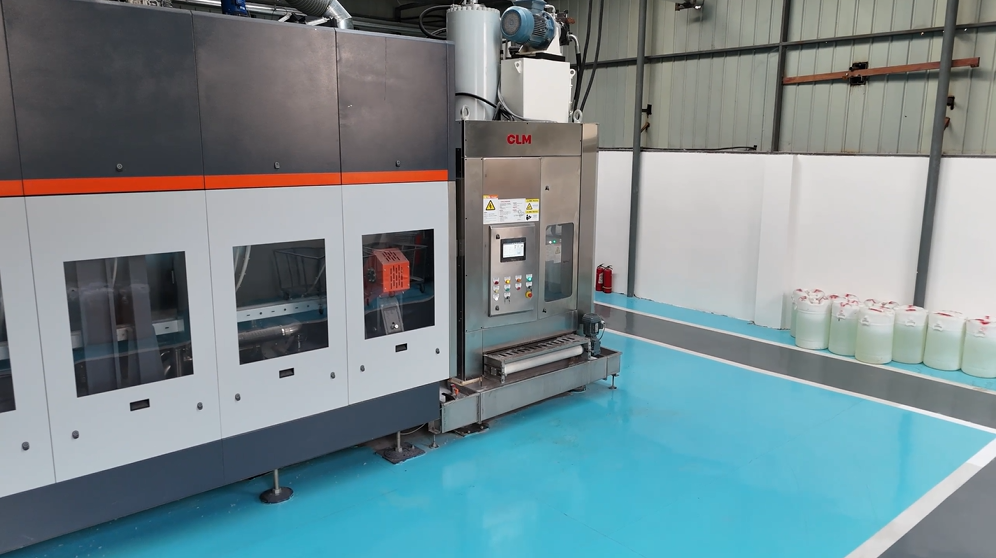
Gas-heated Flexible Chest Ironer: Thermal Efficiency and Environmental Protection
CLM gas-heated flexible chest ironer adopts imported burners. It can burn thoroughly with high thermal efficiency. The gas consumption per hour does not exceed 35 cubic meters. Six oil inlets ensure the rapid and uniform distribution of heat conduction flow, to achieve fast heating, less cold point, saving gas. The interior of all boxes is designed with calcium aluminic acid board to reduce temperature loss and reduce gas energy consumption by at least 5%. Equipped with a thermal energy recovery and utilization system, it can effectively recover heat energy for utilization while reducing the exhaust temperature.
Conclusion
All in all, the Haolan Laundry Plant in Hubei Province, China improves laundry efficiency, reduces energy consumption, and provides strong support for the green transformation of the laundry industry. In the context of energy conservation, emission reduction, and environmental protection, the practices and results of Haolan undoubtedly set a new benchmark.
Post time: Jan-07-2025